Aluminum Foam Suppliers
Aluminum foam is a highly versatile, durable, and efficient material, ideal for a wide range of applications across industries. As a leading supplier and manufacturer, Gerald and Son is dedicated to delivering top-quality aluminum foam products, including panels, tubes, and custom solutions designed to meet your specific requirements.
Our aluminum foam stands out for its lightweight structure, excellent energy absorption, and impressive thermal and acoustic insulation properties, making it a preferred choice for architectural, industrial, and automotive applications.
With a commitment to quality and customer satisfaction, we ensure that every product meets the highest standards. Contact Gerald and Son today to receive a detailed quote or to learn more about the benefits and applications of our aluminum foam products.
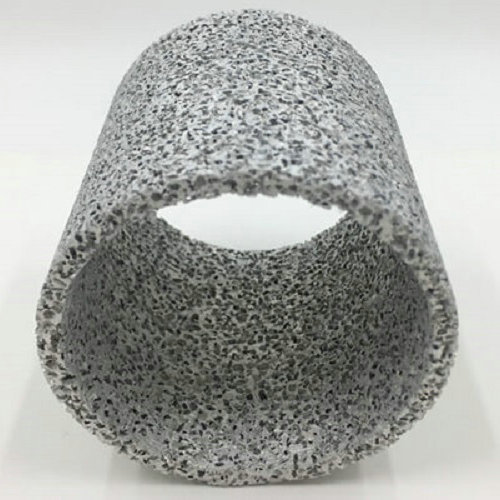
Aluminum Foam Price, please free to contact us.
Aluminum metal foam is a cutting-edge material known for its lightweight structure and exceptional mechanical properties. Produced by infusing aluminum with a foaming agent, this innovative material offers a unique combination of strength, durability, and reduced weight, making it perfect for diverse industrial applications.
Whether you're looking for enhanced energy absorption, thermal insulation, or soundproofing, aluminum foam is a versatile solution that delivers outstanding performance across various industries.
Reach out to us today for:
- Aluminum Foam Pricing
- Stock Availability
- Custom Options** tailored to your project needs
Let us help you find the perfect aluminum foam solution for your application!
Aluminum Foam
Gerald and Son holds over 60 independent intellectual property rights and more than 10 invention patents, showcasing our innovation and leadership in technology. We have developed ultra-high-power continuous electromagnetic shielding technology, offering core technical support for groundbreaking scientific research, including the EAST “artificial sun” controllable nuclear fusion test device. Our products have also been used in prestigious projects, such as providing architectural decoration materials for the Olympic Hockey Hall. With applications spanning across aerospace, bulletproof and explosion-proof industries, ship manufacturing, transportation facilities, vehicle manufacturing, building decoration, and civil composite panels, Gerald and Son is committed to providing advanced solutions for a wide range of sectors.
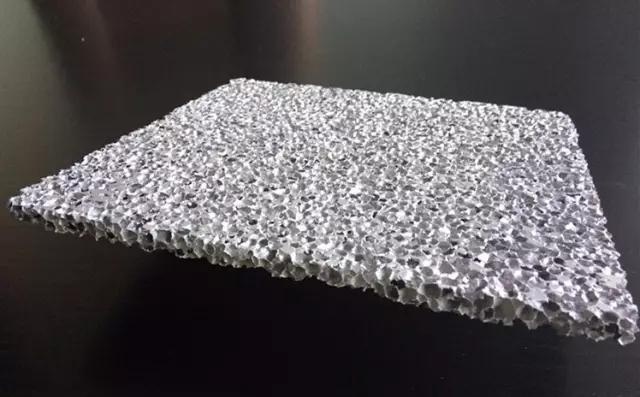
Gerald and Son specializes in the production and customization of aluminum honeycomb, aluminum sponge, and aluminum-covered foam panels in various specifications and sizes. We offer tailored solutions to meet your unique project requirements, ensuring high-quality materials for a wide range of applications. Whether you’re looking for lightweight, durable panels for structural or decorative purposes, we provide products designed to deliver superior performance and efficiency. Contact us today for more details or to request a custom solution!
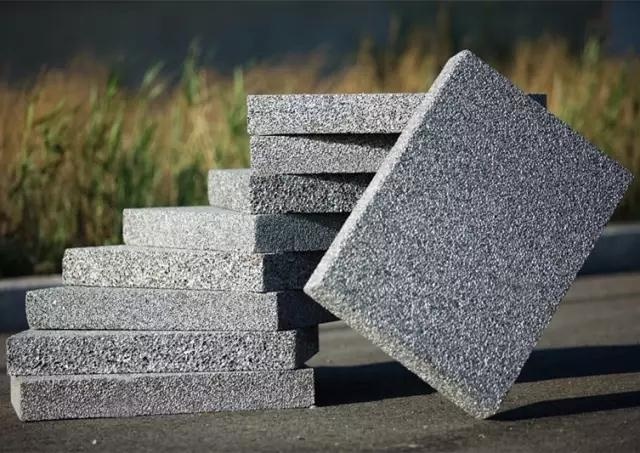
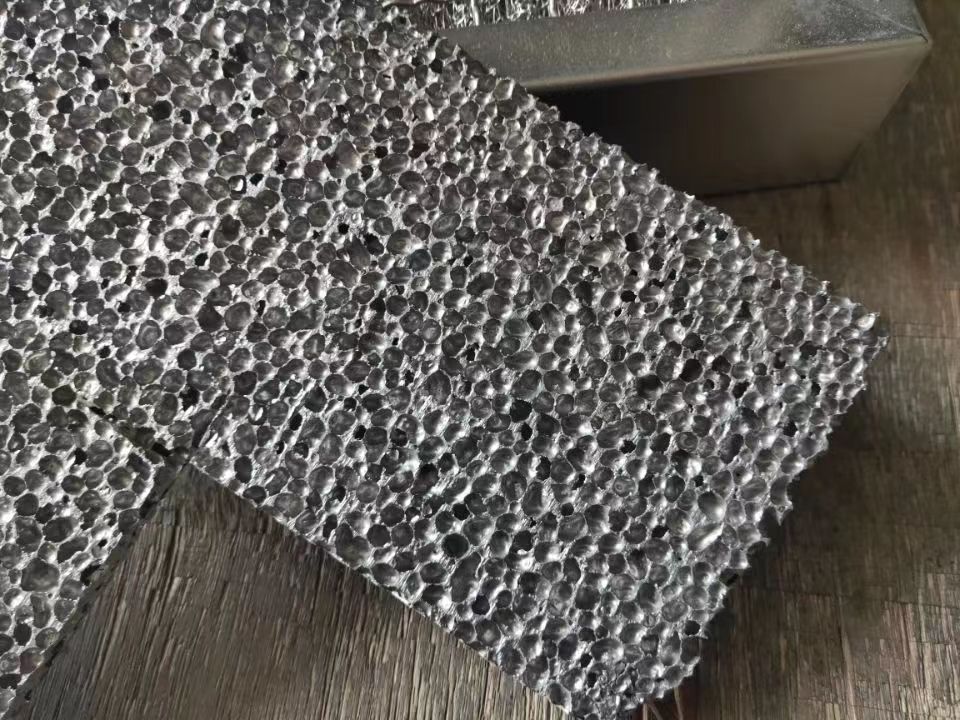
What is Aluminium Foam?
Aluminum metal foam, also referred to as aluminum foam panels, is created by adding additives to pure aluminum or aluminum alloy during a foaming process. In simple terms, it is a metal plate with numerous internal holes, giving it a lightweight structure while maintaining strength and durability. This unique material offers excellent mechanical properties, making it ideal for various industrial applications such as energy absorption, thermal insulation, and soundproofing.
Foamed aluminum, depending on the control during the production process, can have different surface styles, including single-sided open cell, double-sided open cell, and closed-cell configurations. Additionally, foamed aluminum can be customized in a variety of colors. In addition to its natural aluminum color, it can be made vibrant through metal treatment processes like spraying.
Thanks to its unique production process, foamed aluminum offers a wide range of styles and applications. It is an ideal material for architectural decoration, including use in exterior walls, interior walls, ceilings, floors, and staircases, providing both aesthetic appeal and functional benefits.
The Physical Characteristics of Gerald and Son Aluminum Foam (8% nominal density, 6101-T6)
Compression Strength | 367 psi | (2.53 MPa) |
Tensile Strength* | 180 psi | (1.24 MPa) |
Shear Strength* | 190 psi | (1.31 MPa) |
Modulus of Elasticity (Compression)* | 15 × 103 psi | (103.08 MPa) |
Modulus of Elasticity (Tension)* | 14.6 × 103 psi | (101.84 MPa) |
Shear Modulus | 2.9 × 104 psi | (199.95 MPa) |
Vickers Pyramid Number | 35 HV | |
Specific Heat | .214 BTU/lb-°F | (.895 J/g-C) |
Bulk Thermal Conductivity | 3.4 BTU/ft-hr-F | (5.8 W/m-C) |
Coefficient of Thermal Expansion (0-100°C) | 13.1 × 10-6 in/in–F | (23.58 × 10-6 m/m–C) |
Bulk Resistivity | 2.84 × 10-5 ohm – in | (7.2 × 10-5 ohm – cm) |
Melting Point | 1220°F | (660°C) |
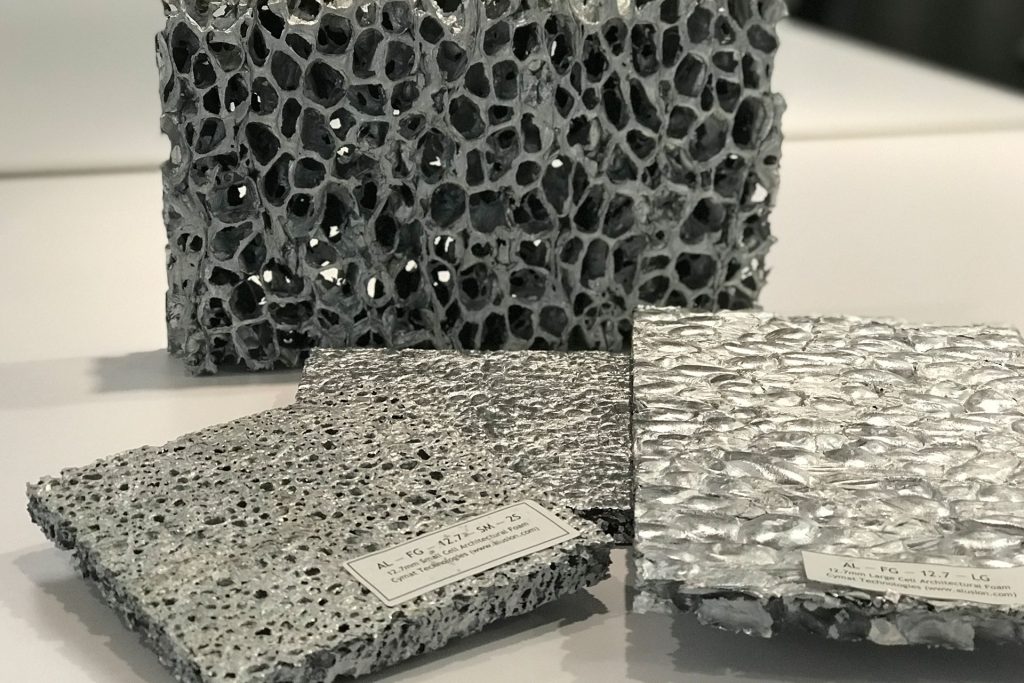
Performance Characteristics of Aluminum Metal Foam
Aluminum foam has a density that is approximately 1/5 to 1/10 of pure aluminum, 1/20 of iron, and 1/4 of wood and plastic. Despite its lightweight nature, its bending stiffness is 1.5 times greater than steel, making it an exceptionally strong material for a range of applications. This unique lightweight panel is particularly well-suited for use as a building skin, providing both strength and energy efficiency. Additionally, aluminum foam panels are completely recyclable, making them an environmentally friendly choice.
Initially used in the automotive industry to reduce vehicle weight and improve fuel efficiency, foamed aluminum has since expanded into the field of architectural decoration. Its versatility and performance continue to make it an ideal material for a variety of industries.
Thanks to the exceptional weather resistance of foamed aluminum, it offers high cost-effectiveness over the building’s life, with reduced service and maintenance costs. Laboratory tests have shown that aluminum foam can withstand exposure to oceanic environments for up to one year without any noticeable deterioration. The surface can be further treated with anti-corrosion sprays to enhance its resistance.
Foamed aluminum has a 0.0% moisture absorption rate, ensuring that it doesn’t absorb moisture, which helps maintain its acoustic performance over time.
Additionally, testing by the National Fireproof Building Material Quality Supervision and Inspection Center confirms that aluminum foam meets the A1 combustion performance level. The material also has a linear expansion coefficient of 19.34 × 10⁻⁷°C, similar to concrete, making it highly stable and resistant to deformation when exposed to heat.
As a foam material, foamed aluminum has excellent thermal insulation effect. The insulation effect of closed-cell aluminum foam is equivalent to that of marble, and the weight is less than half of marble.
At the same time, it has a good acoustic function. The sound insulation coefficient of closed-cell aluminum foam is above 0.9. The sound absorption coefficient of through-hole aluminum foam can reach 0.8.
For office buildings, a space with more cluttered signals can have a good electromagnetic shielding effect. When the electromagnetic wave frequency is between 2.6-18GHZ, the electromagnetic shielding ability of foamed aluminum can reach 60-90dB.
Aluminum Foam Applications
Aluminum foam is a cutting-edge lightweight metal material created using bionic structure principles and aluminum alloy foam. It is characterized by its low density, high specific strength, and a wide range of exceptional properties. These include sound insulation, noise reduction, electromagnetic shielding, energy absorption and buffering, as well as combustion and explosion resistance. Due to these qualities, aluminum foam is extensively used in various industries such as aerospace, equipment manufacturing, transportation facilities, building decoration, and civil panels. Its versatile applications and remarkable performance make it a sought-after material in many modern engineering and architectural projects.
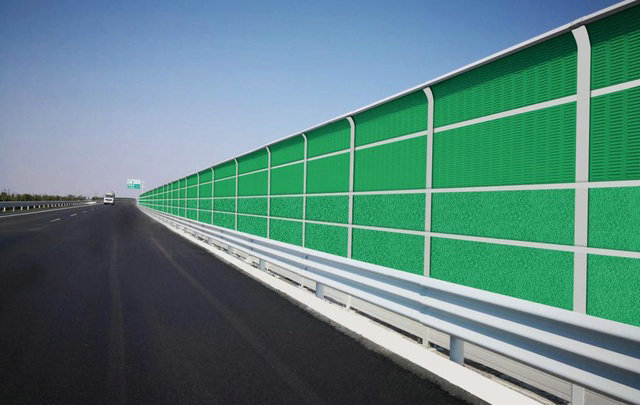
High-Speed Sound Barrier
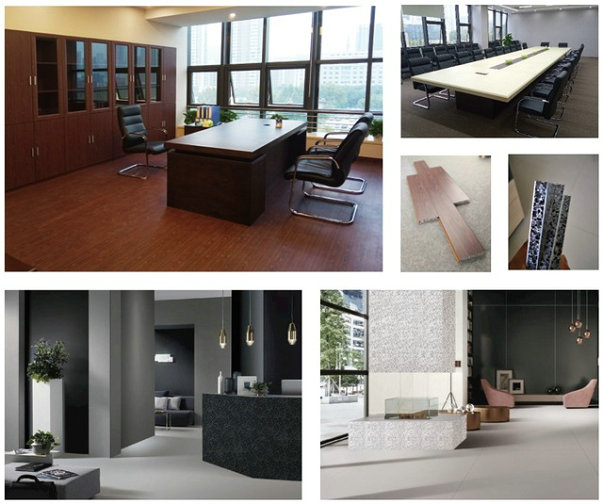
Foam Aluminum Home
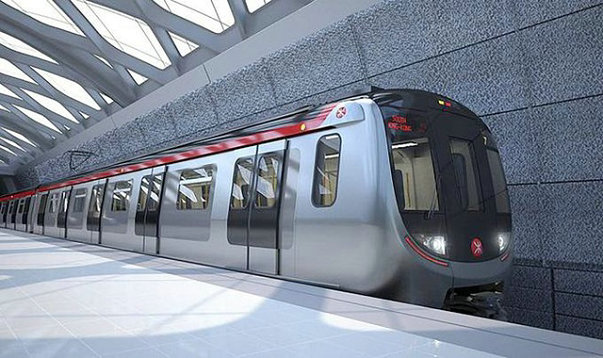
Subway Noise Barrier
How to Make Aluminum Foam?
Aluminum foam is a lightweight, porous material that has many useful properties, such as high strength-to-weight ratio and good thermal and acoustic insulation. Here is a general process for making aluminum foam:
Preparing the aluminum: The first step is to melt the aluminum using a furnace or other heating method. Once the aluminum is melted, any impurities or gases must be removed to ensure a high-quality foam.
Adding a foaming agent: A foaming agent is added to the molten aluminum to create gas bubbles within the liquid metal. There are several different types of foaming agents that can be used, including titanium hydride, calcium carbonate, and aluminum powder.
Casting the foam: The foamed aluminum is then poured into a mold or shaped using other methods, such as extrusion or injection molding. The foam can be made in a variety of shapes and sizes, depending on the application.
Cooling and solidification: Once the foam is cast, it must be allowed to cool and solidify. The cooling process can be controlled to achieve a desired level of porosity and density.
Finishing: The foam may require some finishing, such as trimming or sanding, to achieve the desired shape and surface finish.
Overall, the process for making aluminum foam can be complex and requires specialized equipment and expertise. However, the resulting material can be extremely useful for a wide range of applications.